I remember meeting Josh Alton shortly after he moved south from Northern California to begin working for Horizon Hobby, and because I was racing for Team Losi at the time we already had the catalyst to form a good working relationship - especially because we were both a good mix of serious and hilarious. We both left around the same time, as he took over the head of Hot Bodies' R&D department while I headed for my first publishing job with Hi-Torque's R/C Car Magazine at the end of the 2007 season. I had finished well enough at the ROAR Nationals that year to qualify for the 2008 IFMAR Worlds, and because I had just tested Josh's brand new D8 for the magazine and enjoyed it, he offered to work with me on a feature where I was the only member of the media to race at that Worlds - as a member of his Hot Bodies team. Not only did he help me prepare a car and secure the proper running equipment for the race - engines, tires, everything - and wrench for me, but I spent a couple of nights at his house weeks before the trip so that we could practice and test at Thunder Alley.
See the geek in the back? Thank goodness I've long since shaved off the goatee and started wearing contacts. Thank you to Neobuggy.net for the photo.
The race, for me, was a disaster. I was among the lucky dozens of racers exceptionally screwed by the torrential rain, and then spent the week fighting electronics gremlins to a spectacular 156th place finish (and my co-workers teased me about that for years). As it turned out, I was the only one of five of Josh's D8 buggies not to make the final - and Atsushi Hara put together a brilliant 60-minute final to give Josh's creation its first World Championship.
Josh (right) with Atsushi Hara (middle) and his mechanic, Masayuki Miura (left). Thank you to RCSpecial.com for the photo.
Six years later, Josh Alton's career has taken a couple of turns, including a stop at Team Associated where he spearheaded the development of a new RC8 prototype that never came to fruition. Now having founded his own brand, Alton Design Innovations, I shot him an email to catch up on how he's doing, what he thinks of the ever-evolving RC world, and find out more about ADI.
Aaron Waldron: How did you get started in radio control?
Josh Alton: My RC racing carrier started when my dad took me to Innovation Raceway in San Jose, CA for my 14th birthday. I was hooked! We raced every club race for the next year.
The ADI Losi 8 3.0 D-Pivot, #10047, is made in-house, from 6061 aluminum with the ADI logo engraved. This new pivot uses the kit plastic inserts and has a lower roll center. The lower roll center helps to create more grip and stability through the bumps. It has been tested by our local fast guys and has shown a definite improvement in overall handling and lap times. The setup changes consisted of removing the rear droop screws and running full droop; 118mm shock length. The insert for the C-Pivot used the 1mm insert in the down position. The front half of the bottom rear a-arm had to be lightly dremeled to clear the chassis.
AW: Was RC racing always a hobby, or did you take it seriously?
JA: RC racing has always been a hobby. A serious hobby.
AW: What are your favorite racing classes?
JA: My favorite racing classes are 1/8th scale on-road and off-road.
AW: When did you decide to pursue the RC industry as a career option?
JA: I always knew I wanted to design my own RC cars. As a hobbyist, I would think of ways to improve the design, get a faster lap time, and modify my car. I enrolled at my local community college and transferred to UC Berkeley where I received my degree in mechanical engineering so that I could understand design. All through university I raced and designed for RC racing; I even built a RC engine dyno for one of my class projects! Since graduation I have been fortunate enough to work in the industry doing exactly what I set out to do.
The ADI B5M Chassis Brace 25mm Fan Mount 3D Print, #10037, is made in-house, from ABS plastic, with our Stratasys 3D printer. Most 25mm fans can be mounted to this 3D printed chassis brace. A 3rd party body must be used to ensure proper clearance of the fan. The stock body will not fit properly without modifications.
AW: What was your first full-time job in the RC world? Can you tell us a little bit about the path you’ve taken since?
JA: I was racing a lot of 1/8th scale on-road and met Gil Losi Jr. and Ron Rossetti. Jr. told me to give him a call when I was finished with school. He gave me my first job in the RC industry. I learned a great deal from Horizon Hobby/Team Losi Racing. This education in the field provided me with the tools I needed to accept new challenges and opportunities with Hot Bodies and Team Associated. I have been able to expand my role as a designer and learn from legends in the industry with each opportunity and company. I have increased my design versatility working on many projects both racing and RTR encompassing all types of racing classes.
AW: What products have you been responsible for producing? Are there any you are particularly proud of?
JA: I worked on the Losi LST2, Muggy, Micro-T, Mini Slider, and a few parts on 8IGHT. At Hot Bodies I was responsible for producing the D8, D8T, and Ve8. I am most proud of the LST2, Muggy, Mini Slider, D8, D8T and Ve8.
The ADI Losi 22-4 Carbon Fiber Front Shock Tower, #10034, is made in the USA from 4mm woven carbon fiber. It is a direct replacement for the stock plastic shock tower. It incorporates all the standard shock and camber link mounting locations. Please be sure to seal the edges with cyanoacrylate (CA) glue or clear nail polish to help prevent the edges from delaminating.
AW: It’s easy for those on the Internet to speculate about the business side of RC. What do you think is the most often misunderstood part of producing new vehicles?
JA: Most, if not all, people do not understand the amount of detail and restrictions that go into designing and producing a RC car. Before I started working in the RC industry I would modify my cars and say, “Why can’t XYZ manufacturer just do this?” It's just not that easy for too many reasons that will affect the manufacturer’s bottom line. I have been on both sides and can empathize with the keyboard engineers and racers who think it's “just this easy.”
AW: Both your split with Hot Bodies and Team Associated seemed to come at a time when, at least to the public eyes and years, your relationship with each was strained. What happened?
JA: I loved reading and hearing about all speculation, people just want a soap opera where there is none. My departure from Hot Bodies was a calculated move. I did not feel that the current business model was sustainable and I started looking for another job. I connected with Cliff Lett from Team Associated. I was able to work on a couple projects with Team Associated but was ultimately laid off due to budget cuts. Both of these experiences proved to be growing experiences for me and I was able to glean much about the manufacturing process and working with all types of personalities in the industry world.
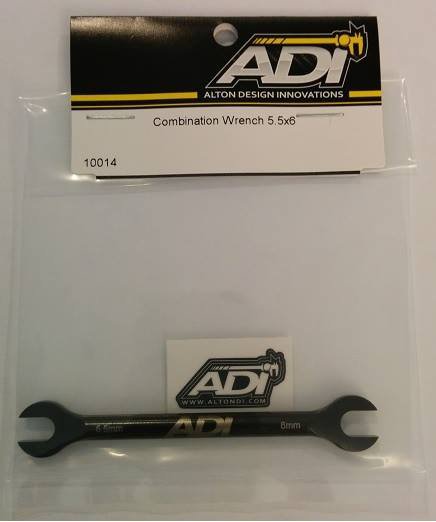
The ADI combination wrench, #10014, is made from machined steel, hardened, and has a black finish with the ADI logo and sizes laser engraved. You wont have to worry about the wrench ends spreading open or changing size after just one use compared to other aluminum wrenches. The ADI combination wrench can be used to adjust 5.5-6mm turnbuckles. The 5.5mm end can also be used with a standard M3 nut.
AW: How do you feel about the role that team drivers play in the research, development, and marketing of new products in the RC industry?
JA: Team drivers can definitely be a benefit and liability. Their role in research and development should be limited because their talent can cloud the testing process. They can mask a problem that the average racer will have. If the problem is not noticed before production then it will be brought up when the average racer gets it and complains online. It's the average racer who pays for their parts and who needs to be happy. The team driver can be a great marketing tool but must be treated as any other employee. Bad attitudes need to be addressed and corrected because they reflect directly on the company. These drivers are on stage every time they are at the track and every explosion is witnessed. True ambassadors of the sport are Adam Drake and Ryan Lutz.
The ADI combination wrench, #10015, is made from machined steel, hardened, and has a black finish with the ADI logo and sizes laser engraved. You won't have to worry about the wrench ends spreading open or changing size after just one use compared to other aluminum wrenches. The 7mm end can be used with the standard M4 nut and some of the nitro engine high speed needle housing. The 8mm end works with the O.S. style nitro engine high speed needle housing. This wrench is a perfect fit in your tool box if you have a 1/5th scale in your RC fleet.
AW: Who have you enjoyed working with the most?
JA: I enjoyed working with Ron Rossetti, Gil Losi Jr., Adam Drake, Todd Hodge, Gary Kyes, Brandon Upshaw, Jesse Robbers, Steve O'Donnell, Barry Baker, Sean Cochran, Curtis Husting, and Kaz Okaguchi. These guys have a great deal of passion for racing and the products they represent.
The ADI combination wrench, #10016, is made from machined steel, hardened, and has a black finish with the ADI logo and sizes laser engraved. You won't have to worry about the wrench ends spreading open or changing size after just one use compared to other aluminum wrenches. The ADI combination wrench can be used to adjust 3-3.5-4mm turnbuckles.
AW: When did you decide to strike out on your own with the new brand ADI?
JA: I decided to start ADI after I was laid off from AE. I was paid by other manufacturers for my ideas and decided to use my ideas for my own business venture.
AW: What was so appealing about creating your own company? What are some of the biggest challenges?
JA: Having my own company allows me creative autonomy and addressing the products I feel need to be brought to market. I finally am able to be the answer to ‘Why can’t they just …” I also enjoy being able to stay home with my two boys and work in the off hours. The limited hours can be challenging but I tend to work smarter not harder. The initial capital investment is also challenging but necessary.
The ADI combination wrench set, #10020, includes three hardened steel wrenches, #10014, #10015, and #10016.
AW: What’s coming next from Alton Design Innovations?
JA: My initial plan is to start with aftermarket parts for most brands with a goal of my own car in the distant future.
The ADI 17mm hex wheel wrench, #10021, is made of 6061-T6 aluminum and is hard anodized with the ADI logo and size laser engraved. It fits 1/8th electric / nitro vehicles or any 17mm hex nut. It is light weight with a cored handle and center through hole to help with the installation and removal of the screw that holds the wheel hex to the axle.
AW: Thanks for the interview!
JA: Thank you for the interest in me and ADI.
Recent comments